Researchers have created what could be called “skin in a syringe”. The gel containing live cells can be 3D printed into a skin transplant, as shown in a study conducted on mice. This technology may lead to new ways to treat burns and severe wounds.
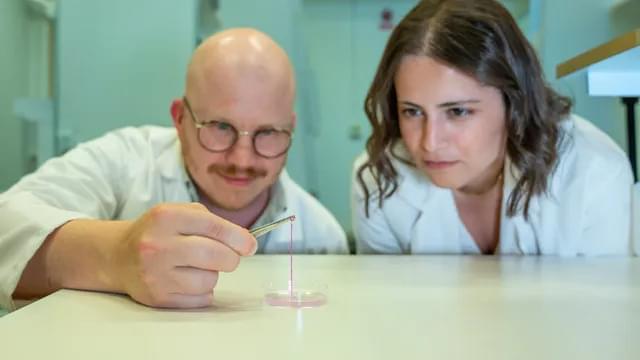
What the hook? 3D-printed joints cut repair costs, prevent construction waste.
Scientists in Austria have developed a new hook-and-loop fastening system that has the potential to dramatically reduce construction waste and make buildings easier to adapt, repair, and reuse.
The innovative component was designed by an interdisciplinary research team at the Graz University of Technology (TU Graz) in the Austrian province of Styria as part of the ReCon project.
Inspired by Velcro, the original hook-and-loop fastener invented in 1948 by Swiss engineer George de Mestral, the novel product enables structural components to be securely connected and easily separated when needed.
3D-Printed Exoskeleton Learns From Your Hand ‘…small electric motors at the principal joints worked the prosthetic framework by means of steel cables…’ — Fritz Leiber, 1968.
Smartwatch Powered By Slime Mold ‘Living protoplasm incorporated into the Ampek F-a2 recording system…’ — Philip K. Dick, 1966.
Carpentopod Walking Table ‘Twoflower’s Luggage, which was currently ambling along on its little legs…’
Over the past decades, energy engineers have been developing a wide range of new technologies that could power electronic devices, robots and electric vehicles more efficiently and reliably. These include solid oxide cells (SOCs), electrochemical devices that can operate in two different modes, as fuel cells or as electrolyzers.
3D printing is a simple way to create custom tools, replacement pieces and other helpful objects, but it is also being used to create untraceable firearms, such as ghost guns, like the one implicated in the late 2024 killing of UnitedHealthcare CEO Brian Thompson.
Netanel Raviv, assistant professor of computer science & engineering in the McKelvey School of Engineering at Washington University in St. Louis, led a team from the departments of Computer Science & Engineering and Biomedical Engineering that has developed a way to create an embedded fingerprint in 3D-printed parts that would withstand the item being broken, allowing authorities to gain information for forensic investigation, such as the identity of the printer or the person who owns it and the time and place of printing.
The research will be presented at the USENIX Security Symposium Aug. 13–15, 2025, in Seattle. The first authors of the paper are Canran Wang and Jinweng Wang, who earned doctorates in computer science in 2024 and 2025, respectively. The research is published on the arXiv preprint server.
Researchers at RMIT University in Australia have developed a new form of titanium for 3D printing that costs approximately 33% less than the titanium alloys currently in widespread use.
Replacing expensive elements
The researchers substituted vanadium, which has become increasingly costly, with more affordable and widely available alternative elements.
In recent years, 3D printing glass optics has gained massive attention in industry and academia since glass could be an ideal material to make optical elements, including the lens. However, the limitation of materials and printing methods has prevented 3D printing glass optics progress. Therefore, we have developed a novel printing strategy for germanate glass printing instead of pure silica. Moreover, compared with traditional multi-component quartz glass, germanate glass has unmatched advantages for its mid-infrared (MIR) transparency and outstanding visible light imaging performance. Furthermore, compared with non-oxide glass (fluoride glass and chalcogenide glass), germanate glass has much better mechanical, physical, and chemical properties and a high refractive index.