Israeli scientists are using 3D printing to reconstruct damaged coral reefs.
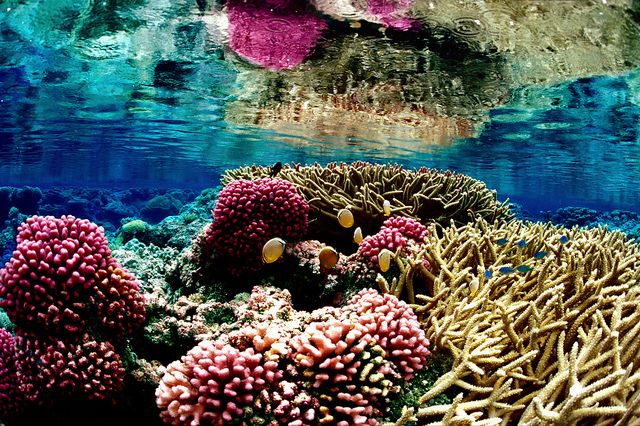
The 19 3D-printable parts that make up the mask are visible on the Maker Mask website along with details on materials needed, download instructions, videos, the ability to donate to the cause and more. The cost of each finished mask, printed in about three hours, is estimated to be between $2 and $3.
A technology veteran and a 3D-printing “savant” have teamed with other members of industry, health care and government to launch Maker Mask, a Seattle nonprofit creating medically endorsed, reusable protective masks using everyday 3D printers.
Jonathan Roberts, founder and partner at the Bellevue, Wash.-based venture capital firm Ignition Partners, is also a co-founder of RPrime, a nonprofit that is helping to fund the mask-making initiative. The former Microsoft executive said the goal is to address critical supply shortages and support “the real heroes on the front lines” of the COVID-19 pandemic.
The respirator-style mask with a replaceable HEPA filter and other commonly available parts, was developed by Rory Larson, a rapid prototyping expert with 10 years experience in engineering, CAD, 3D printing, CNC and small batch production manufacturing. It took just a week for the group, working with Larson’s design, to get a small production facility up and running out of Epiphany Parish in Seattle.
If you’ve never heard of a tensegrity structure, you should stop now and watch the video below. In it, [The Action Lab] shows a 3D printed table that is held up only with strings. We didn’t say suspended by strings but held up. Or so it appears. The model is from Thingiverse, but it is one of those things you have to see to believe.
The basic idea is pretty simple. Strings have a lot of tensile strength but collapse under the slightest compressive force. The arrangement of strings puts the force on the center string which is essentially hanging — the force is pulling the string down. The other three strings aren’t just for show, though, they keep the structure from tipping over in any one direction.
There are actually real-life examples of these kinds of structures. The video shows the Skylon at the Festival of Britain as one example and an Australian bridge. The video also makes the point that the human body uses tensegrity, since tendons are very similar to the strings in the model.
When you’re a software and hardware engineer sometimes you need a little challenge. Engineer Robert Lucian Chiriac’s latest Raspberry Pi creation can detect license plates and read the characters with fairly decent accuracy. This is an involved project that relies on machine learning to properly interpret images from the camera into discernible text.
The primary license plate reading function is constructed using three separate applications (there are more used throughout the project, but these three are critical). Chiriac used the YOLOv3 object detection algorithm to create a bounding box around each license plate it detects from the camera input. The image within the bounding box is sent to CRAFT, a text detecting application. Once the location for each character in the plate has been identified, the information is passed along to CRNN to predict the actual text.
Chiriac mounted the Raspberry Pi, GPS module, 4G module and Pi camera to his car’s rear-view mirror with a 3D-printed unit he designed. The Pi camera is even adjustable with a ball-joint swivel mount.
World’s Largest 3D Printer re: Philip K. Dick on 3/1/2020: Science Fiction in the News.
Topline: A group of 300-plus engineers, designers, tech founders and others galvanized on Facebook with a goal of building a ventilator using readily available materials, 3D printing and open-source hardware resources. In just seven days, they built a prototype that will be validated as a solution to the global ventilator shortage by Irish authorities as early as next week.
Dreams of human immortality may remain so, but extending our lives beyond 100, even 150 years, can soon become a reality. ‘The Future is Now’ explores ground-breaking technology that might help us to slow down the ageing process and overcome our physical limitations.
3D-printing of brand new human organs, controlling bionic prosthetics with your mind, or invading your body with disease-fighting microrobots. Hosts Kate and Talish bring you the latest developments in biomedical engineering.
Learn what artificial organs have to do with gravity, or see how the world appears to blind people who have had their vision restored with bionic eyes and a chip. Hear from researchers and futurists about their predictions and warnings regarding the future of science.
SUBSCRIBE TO RTD Channel to get documentaries firsthand! http://bit.ly/1MgFbVy
FOLLOW US
RTD WEBSITE: https://RTD.rt.com/
RTD ON TWITTER: http://twitter.com/RT_DOC
RTD ON FACEBOOK: http://www.facebook.com/RTDocumentary
RTD ON INSTAGRAM https://www.instagram.com/rtdocumentaries/
RTD LIVE https://rtd.rt.com/on-air/