A construction company printed an entire house in 24 hours and it only cost $10,000.
Category: 3D printing – Page 90
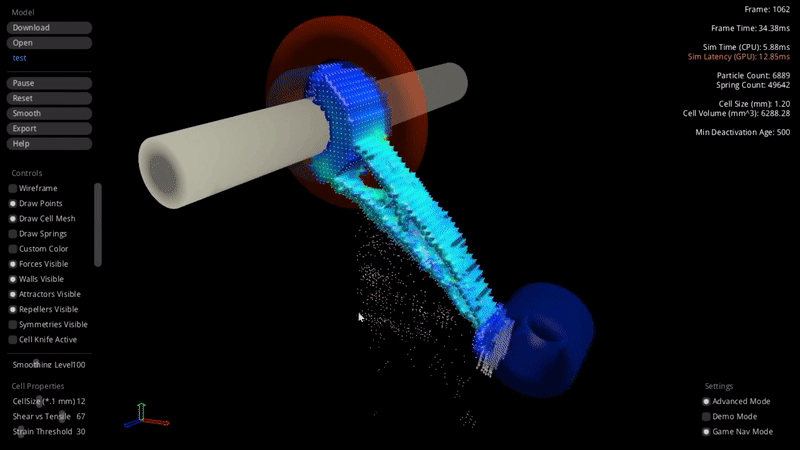
This AI software dreams up new designs for 3D-printed parts before your eyes
Desktop Metal’s new software lets regular people design objects optimized for 3D printing, no experience required.
The news: Desktop Metal’s new LiveParts is a piece of software that automatically generates designs of objects ready for 3D printing. Users just tell it the structural constraints of the object they’re building, and it uses biology-inspired AI models to quickly generate a design suited to additive manufacturing.
Better components: The software ensures that parts take advantage of 3D printing’s capabilities. “This would enable weight reductions between 25 and 60 percent of many kinds of general-purpose parts,” says Desktop Metal CEO Ric Fulop, “while spreading loads more evenly and improving fatigue resistance.”
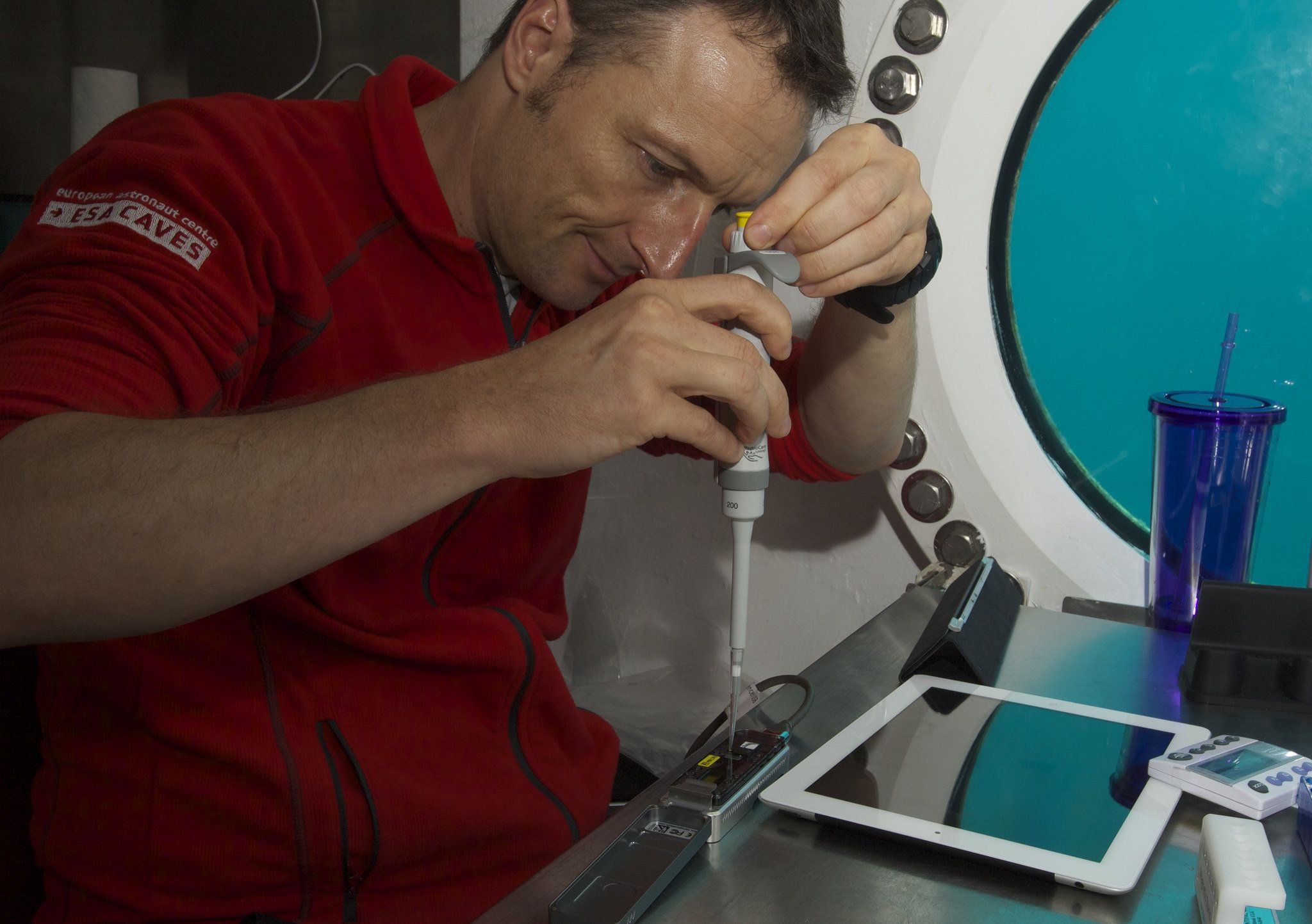
3D printable tools to study astronaut health
If humans are destined for deep space, they need to understand the space environment changes health, including aging and antibiotic resistance.
A new NASA project could help. It aims to develop technology used to study “omics”—fields of microbiology that are important to human health. Omics includes research into genomes, microbiomes and proteomes.
The Omics in Space project is being led by NASA’s Jet Propulsion Laboratory in Pasadena, California. The project was recently funded by NASA’s Translational Research Institute for Space Health four years of study. Over that time, NASA hopes to develop 3D printable designs for instruments on the International Space Station (ISS), that can handle liquids like blood samples without spilling in microgravity. These tools could enable astronauts to analyze biological samples without sending them back to Earth.
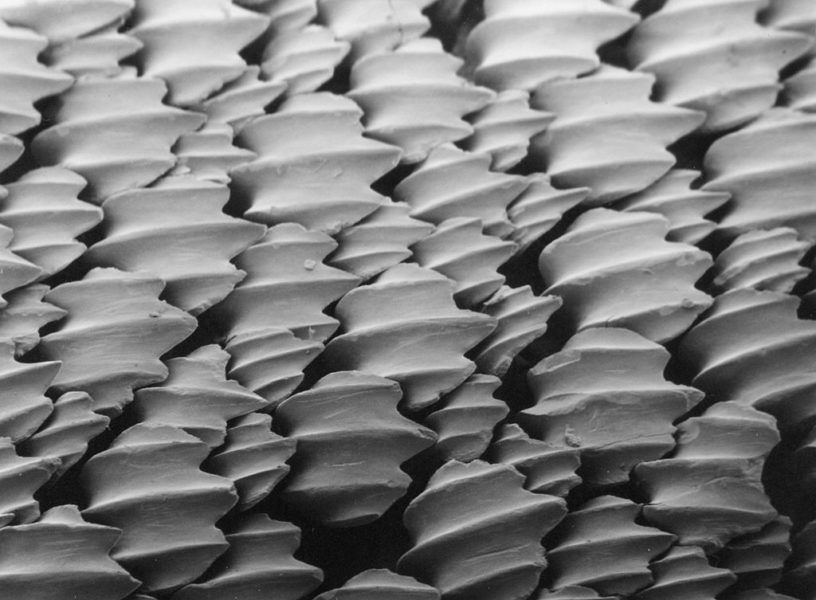
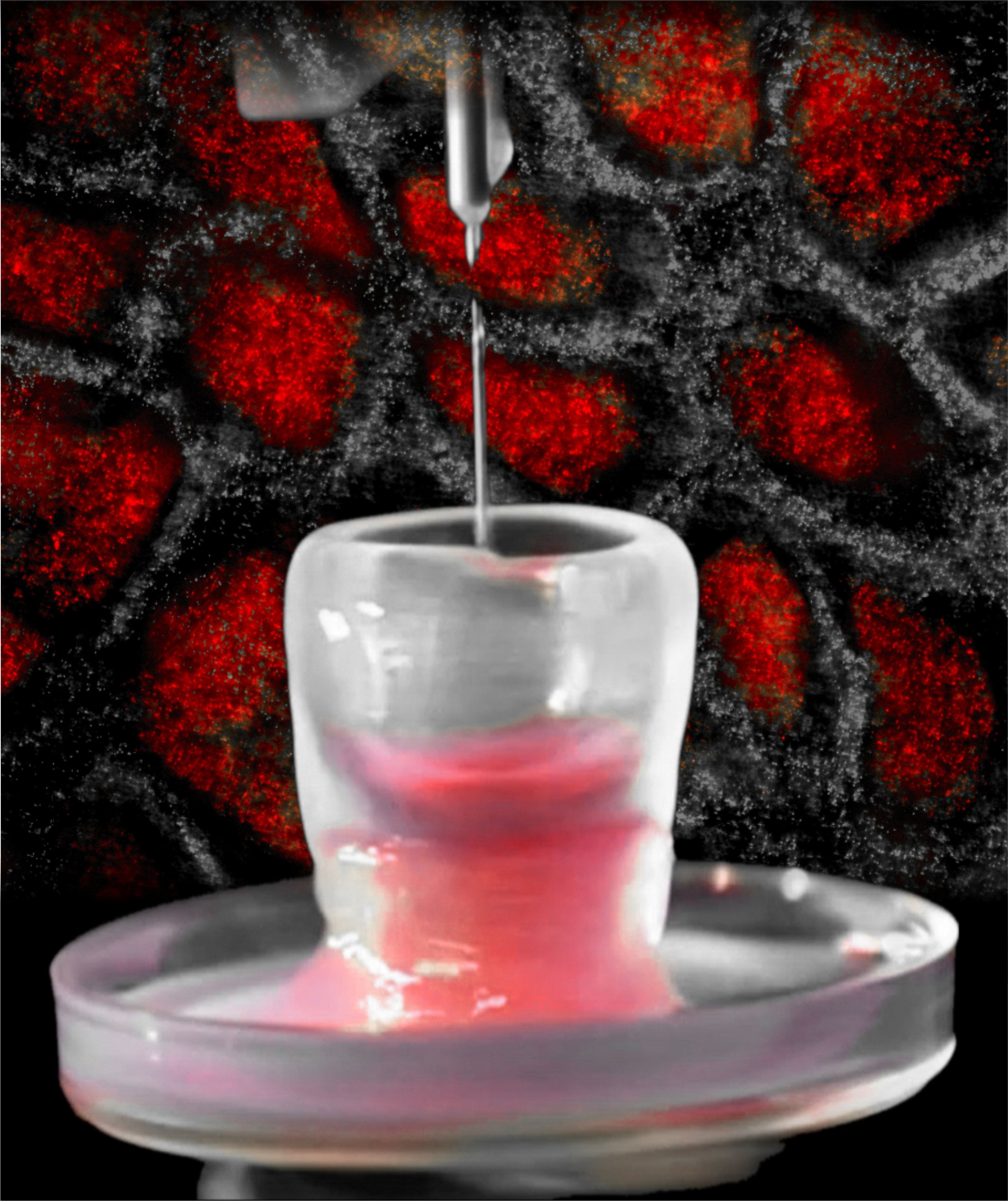
3D printing of living cells
Using a new technique they call “in-air microfluidics,” University of Twente scientists succeed in printing 3D structures with living cells. This special technique enable the fast and ‘on-the-fly’ production of micro building blocks that are viable and can be used for repairing damaged tissue, for example. The work is presented in Science Advances.
Microfluidics is all about manipulating tiny drops of fluid with sizes between a micrometer and a millimeter. Most often, chips with tiny fluidic channels, reactors and other components are used for this: lab-on-a-chip systems. Although these chips offer a broad range of possibilities, in producing emulsions for example—droplets carrying another substance – the speed at which droplets leave the chip is typically in the microliter per minute range. For clinical and industrial applications, this is not fast enough: filling a volume of a cubic centimeter would take about 1000 minutes or 17 hours. The technique that is presented now, does this in a couple of minutes.
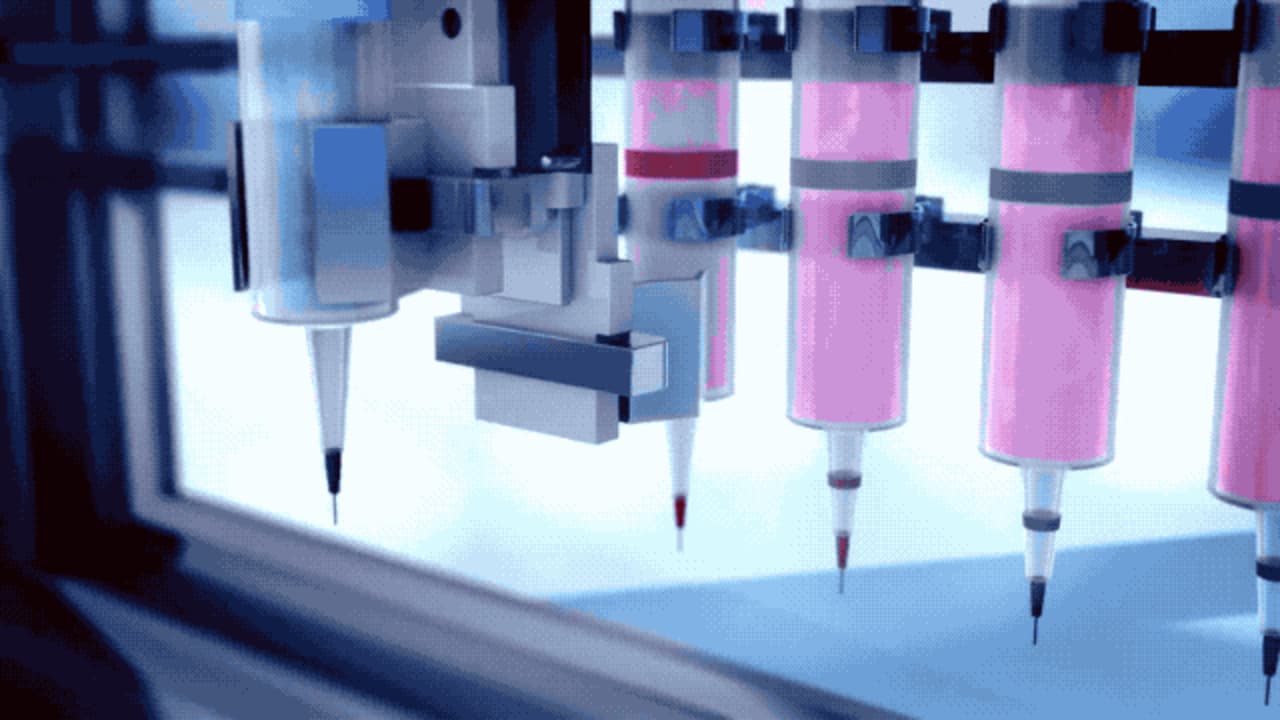
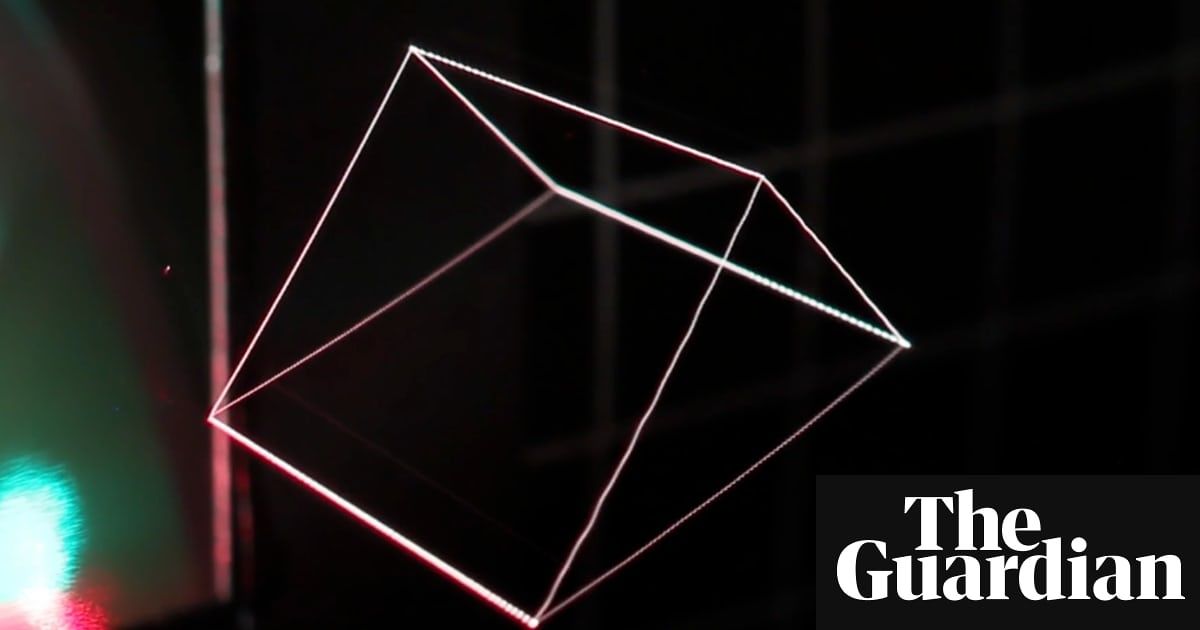
‘Floating 3D printing’ brings sci-fi-style projections closer
‘Optical trap display’ projects graphics into the air, where they are visible from all angles.
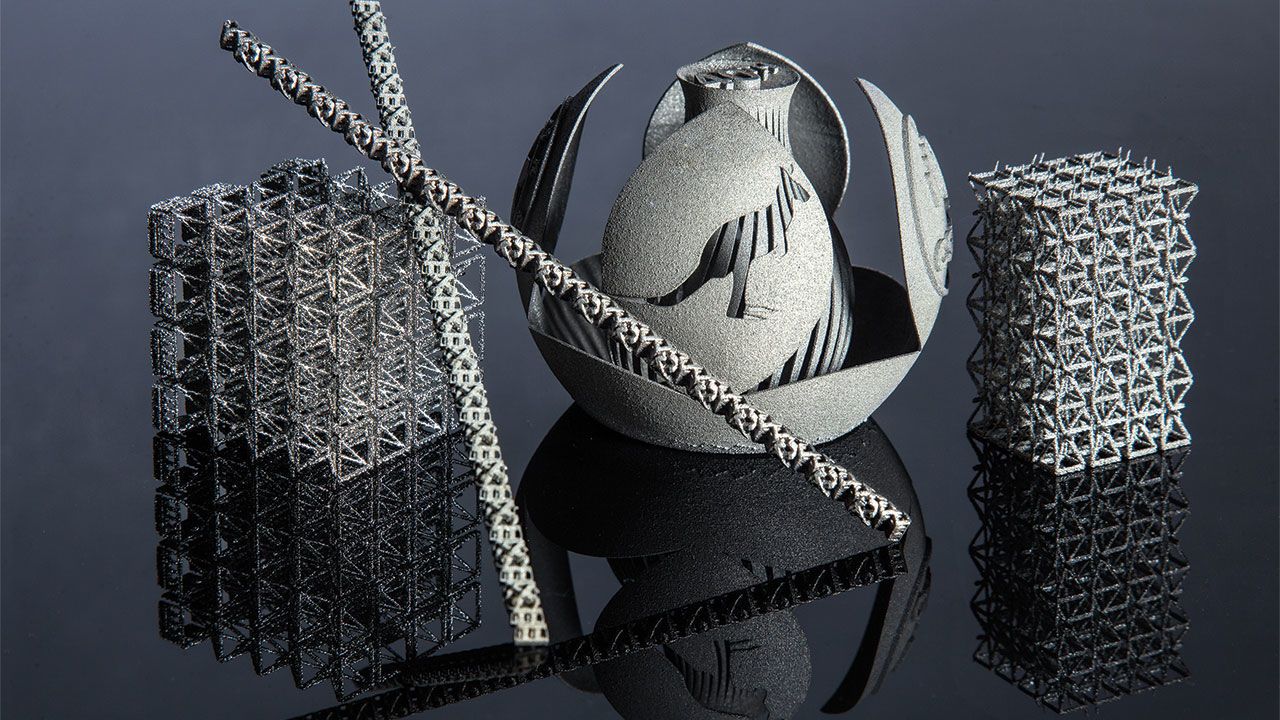
You could soon be manufacturing your own drugs—thanks to 3D printing
But it remains to be seen whether drug regulators will go along with a new way of making medicines. To do so, agencies like the U.S. Food and Drug Administration will need to rewrite their rules for validating the safety of medicines. Instead of signing off on the production facility and manufactured drug samples, regulators would have to validate that reactionware produces the desired medication. Cronin agrees it’s a hurdle. But he argues that future printed reactors could simply include a final module containing standard validation tests that produce a visual readout, much like a pregnancy test. “I think it’s manageable.”
Digitized chemistry on demand could also undermine drug counterfeiters.
Army Grapples With Cyber Age Battles In Megacities
High-tech warfare at knife-fight ranges: that’s the ugly future of urban combat. If you thought Baghdad was bad, with its roughly six million people, imagine a “megacity” of 10 or 20 million, where the slums have more inhabitants than some countries. Imagine a city of the very near future where suspicious locals post every US military movement on Twitter with digital photos and GPS-precise coordinates. Imagine roadside bombs that fly because the bad guys downloaded blueprints for a kamikaze mini-drone and built it with their 3D printer.
As the US pulls out of the mountains and deserts of Afghanistan, the Navy and Air Force may be looking to the wide-open Pacific, but the Army is increasingly concerned about the cramped alleyways of Third World cities. (The Marines, as usual, have a foot in both worlds). Chief of Staff Ray Odierno’s personal Strategic Studies Group — now led by hybrid warfare expert David Johnson — is working on the subject, as is the Army’s think tank and teaching institution, Training and Doctrine Command (TRADOC). This August, after months of seminars, simulations, and study, the Army War College will host a “deep future wargame” set in a megacity, probably a coastal one, circa 2035.
“We talk about the danger of failed states: Imagine a failed megacity,” offers Col. Kevin Felix of TRADOC’s Army Capability Integration Center (ARCIC), which plays a leading role in organizing the wargame. Even a partial breakdown of security and public services could put thousands of people in peril — or under the rule of drug gangs, as in Brazil’s infamous favelas; or of terrorist groups, like Hezbollah in parts of Lebanon. In those parts of the city, Felix told me, “there may be order, but I wouldn’t define it as law and order.”
This 3D-Printed Heart Could Replace Blood Pumps
These 3D-printed, artificial hearts could replace real hearts one day.